Waste management
Dealing differently with waste
As an active participant in the metal industry, there is one thing we cannot avoid: we create waste. And waste has a negative impact on people, animals and the environment. In our striving for greater corporate social responsibility, how we deal with waste forms an important aspect. That is why we are giving you here a glimpse into our waste processing. We describe how we are constantly raising the bar there, for each other and for our future. Would you like to learn more?
Robert van Veen, Facilities Manager, talks about this:
"Steel, aluminium and wood are our largest waste products. We have documented these waste flows and designed a system to stimulate the separation of waste and optimise its disposal. As a result, we need fewer waste transports. We are also striving to curb the quantity of waste created, because if you don’t produce it, you do not have to dispose of it of course."
Waste containers
There are recognisable containers located in each of the 12 factory halls. In the offices all individual waste bins have been replaced by central containers for separated collection. Recently, we got a new glass recycling bin and our container that separates plastic, metal and drinking cartons, has been replaced for a container that separates plastic and drinking cartons.
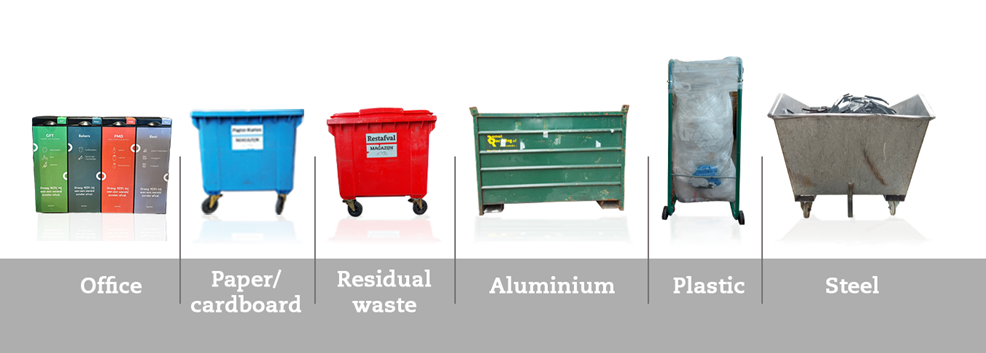
Steel, aluminium, and wood
Steel / Aluminium
At 180,000 kg per year, steel/aluminium is our biggest waste product. We separate aluminium into four categories, according to reusability. Each category has another yield. The available containers for them are positioned right next to the machines that produce the waste.
In the new production halls in Monster, we have installed underground, automatic disposal systems for machine waste. This allows us to capture the waste immediately and keep it separate from other waste flows. Recycling becomes easier as a result.
Wood
Wood is an important packaging material, and every transport from and to our company produces wood waste. On an annual basis this amounts to around 120,000 kg. We found a solution for this that is rather uncommon in our industry: we purchased a roll packer!
Robert explained, "This roll packer chops up and compacts the wood waste. This has led to a large reduction in the wood transport needed: previously this was every ten days, but now it is just six times a year. We save money, but even better we lower our CO₂ emission."
How does Robert envisage the future?
"We shall keep advancing one step at a time. For our new building on the Galgeweg in ‘s-Gravenzande, we are doing our best to separate everything as efficiently as possible. In other words, the end is nowhere in sight for these sorts of developments!"